For many years, workers at the Cardinal Health manufacturing facility in Waukegan, Illinois, packed sealed cases of packaged surgical tools into 0.076 mm (3 mil) low-density or linear low-density polyethylene bags. Then seal the bag with tape. Because bags are torn or torn on existing conveyor systems, these bags are loaded on pallets and manually transported to the company's stretch packaging, storage, and transportation departments. Labor costs remain high. The company also believes that labelled boxes packaged in bags are not attractive to their hospital customers, who have to identify these packages before they are stored in the central supply area.
"These tools are used in the operating room," explained Jeff Cavil, senior chief engineer at McGaw Park. “We cannot allow boxes that have been contaminated by the transport environment to enter the operating room. Therefore, before being delivered to a central area, which is usually located in a hospital clean room, it is necessary to use a thin film wound around the outside of the box and the hospital staff will collect it. Removed on shipment."
To solve its packaging problem, as early as last year, Cardinal Health and EDL jointly created a system to integrate the company's conveyors and manufacturing systems.
The main feature of this system is the EDL's double wrapper, which can package each box twice with a 0.038mm low-density polyethylene film, one from the end forward and the other from the side forward. As a result of the double packaging, two layers of film are formed at the corners and under the box. "These areas are typical wear areas of the box and are often accidentally touched," said Cavil.
After the second packaging, the box is transported through a hot air duct that tightly shrinks the film onto the corrugated carton.
The box of the packaging tool is wrapped in a transparent film and is transported downwards by the packaging machine. The transmission system (PBDS) does not cause accidents when it is transferred. The clean and transparent wrapping film also makes the package more attractive to the hospital. Before the clean, white lined box is delivered to the operating room, the hospital staff removes the film and classifies the surgical instruments.
In early 2003, EDL equipment was added not only in Waukegan but also in Cardinal plants in California and New York. Each factory transports surgical tools to hospitals and independent surgery centers in its area.
Cavil explained that each PBDS includes appliances that are required for special operations such as replacement of the arm or knee, caesarean section, or cardiac bypass surgery. "For different surgeries or different hospitals, the same surgical procedure may require different customized appliance products," added project engineer Catherine Heft. Surgical instruments may contain anywhere from 15 to 150 tools. The total weight of surgical instruments is 2.25kg-29.25kg. Tools may include IV bottles, anesthesia subassemblies, surgical and surgical gowns, sutures, suture needles, surgical pumps, mop heads, and even personal items such as shampoos and deodorants. Cardinal
Health manufactures many of these products; others are made by dozens of other leading manufacturers. Before being repackaged by Cardinal Health, some products were pre-packaged on arrival and some were disinfected.
face the challenge
“The change from placing boxes in plastic bags to using automated shrink packaging is driven by comprehensive cost savings, better package appearance, and customer convenience,†said Cavil.
Although Cardinal chose automation, it also has an important tip: "Our job is to make surgical tools, not packaging boxes," he said. "One of our requirements is that running a machine cannot occupy more than 25% of the operator's time, including roll replacement. Therefore, we need a machine that can work independently."
The operator is not professional about the machine. Its main task is to handle packaging materials and products used to make surgical tools.
Cavil said that Cardinal Health “recognized early on that we needed to customize tool equipment to handle different sized boxes and meet our space requirements. An intermittent motion machine must be used because we use random dimensions instead of batches. Don't want to trade in exchange for the machine."
In order to achieve multiple goals, Cavil said that the company "filtered many suppliers." “We found out that EDL has the most modern technology to do this job. Before we accepted the machine, we used our box to perform factory acceptance tests at its factory.†Later, Cardinal
Health purchased three machines, one for each factory.
Pursue the process
In Waukegan, Cardinal Health operated machines to produce double-packed boxes at a speed of about 10 boxes/minute. The surgical tool is packaged in a kraft-lined corrugated carton or in a corrugated carton with a white coated paper surface. Kraft paper lining boxes are used for "conventional products", which are regulated by Cardinal Health as a general supply, such as admission of tools that are not related to the surgical procedure. These boxes do not require shrink packaging. Cavil says the boxes with white coated paper have a cleaner, more attractive appearance. These boxes require shrink packaging to ensure cleanliness before entering the operating room.
Cardinal Health uses computers to print pressure-sensitive labels containing the PBDS type, part number, customer, package name, and any other major details. Workers attach labels to each box. Kraft paper and coated paper boxes are randomly transported along the main roller conveyor to the EDL equipment. A color-sensitive electronic eye reads the reflection coefficient at the back of the box. In the case of a kraft paper box, the loading tray is transported directly downwards. A pop-up roller device temporarily stops the white box before the white box is released onto the conveyor of the input EDL machine. The system allows 4-5 boxes to accumulate in front of the double wrapper. A set of pneumatic clips will bring the incoming box to the conveyor, and the conveyor will send the box to the first workstation. The flight lever pushed the box into a 60.96 cm wide film curtain. The two packaging workstations on the EDL equipment consist of 2 rolls of film, one on the top of the box and the other on the bottom, where it is pushed up through a small gap on the conveyor. The film was sealed by heating to form a film curtain. The box moves upward so that the membrane covers its top, bottom, front and rear edges. As the flying rod descends, the heating anvil rises from the bottom of the box. The two parts meet and heat seal the trailing edge of the film and the leading edge of the film in the next surgical kit. A heating blade in the sealing device cuts the sealing area to separate the packaging box from the film curtain. The flight bar pushes the tightly packed box out of the first packaging station. The box is transported several feet away, docked on a vertical conveyor and sent to the second packaging station. The right-angle conveyor positions the box so that the wider side of the box enters the second workstation seal.
Prior to this sealing, the EDL machine used guides and pneumatics to fold the first layer of film around the eight corners of the box, pushing the film down from the four corners above and pushing the film up from the four corners below.
The second sealing process is similar to the first except that a flying system is used, which uses a pneumatic pushing device. The box enters a 96.52 cm wide film curtain for packaging. After being unloaded from this station, the box is stopped on the vertical conveyor again and this is transferred into the hot air duct.
C ardinal Health closely monitors the temperature of the film sealing and shrinking hot air ducts to keep them within the effective tolerances required by the equipment. Although the box needs to be sent to the main roller conveyor, after the box has just exited the hot air duct, peripheral air blows onto the box to carry the box when necessary. The box is transported to a larger mixing area and then transferred to a suitable support for manual loading of the tray and stretching the wrapping. In general, the hospital's cargo is mixed, some are PBDS surgical tools, some are general supply boxes for kraft paper packaging, some with bottled water and other supplies.
Have advantages
Cardinal Health is extremely satisfied with this equipment and is expected to quickly recoup its investment. Labour cost savings provide most of the returns, but there are other major benefits. "We no longer use 0.076mm bags," said Cavil. “Instead, we use two layers of 0.038mm film packaging. Because the film width is just wider than the size of the box we pack, our film waste is not much more than the original used. However, in the key corner area of ​​the box, we still have 0.076mm. Mm thickness." He also pointed out: "We buy rolls of film cheaper than buying bags."
EDL equipment also saved important space for the Cardinal Health plant. "The device is operating in a U-shaped work chamber," Heft said. "With many shrink packers and duct systems, we may need a 5- to 7.6-meter-long line," Cavil added. "This can be entered in a box, wrapped in one direction, turned in a box, and then wrapped in another direction, so the machine's footprint is more suitable for our work area." But, better yet, he said: "We can There is no hole or tear when the box is delivered to our customers." This is exactly the kind of remedy that Cardinal Health sought.
Single leg Standing Desk is one of our sales products. This single leg has Electric Standing Desk and Pneumatic Standing Desk. This product is very popular at present. We also developed a single leg electric desk under the customer demand. The single leg pneumatic desk has always been very popular because of its high cost performance and small size. It is suitable for adults and children. A small tea table and a temporary operating table are placed beside the sofa in the living room for work, leisure and dining. Sit Stand Desk has the design of universal wheel, which can be moved and placed beside the bed at any time. Users can study and work directly on the bed, and it can be used with the disabled bed.
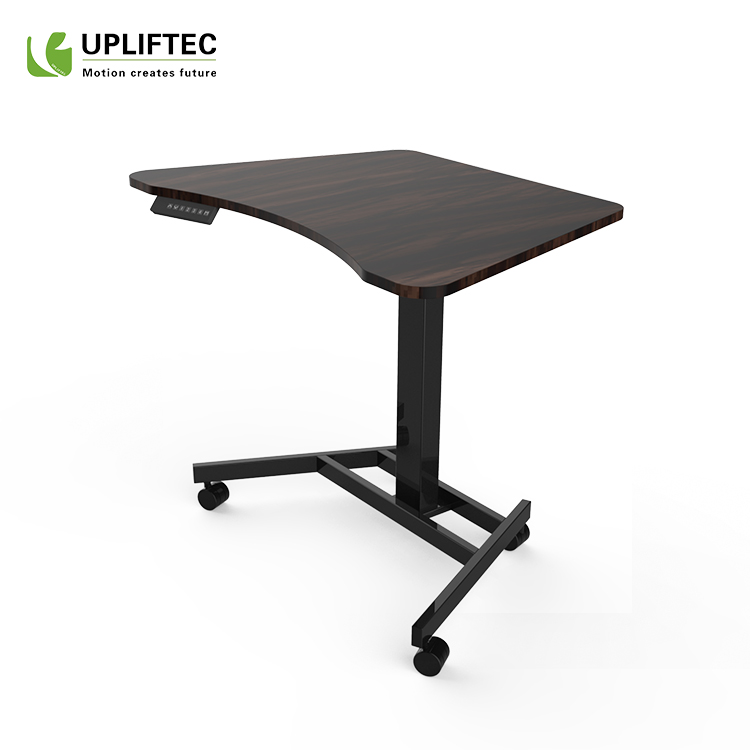
single leg standing desk,standing desk height,adjustable table,Standing Adjustable Desk,sit stand table
Suzhou Uplift Intelligent Technology Co., Ltd , https://www.upliftecdesks.com